Maintenance of Natural Gas Engine for Generator Set
- startlight
- Apr 28, 2019
- 3 min read
Maintenance costs vary with type, speed, size and number of cylinders of an engine. These costs typically include:
• Maintenance labor
• Engine parts and materials such as oil filters, air filters, spark plugs, gaskets, valves, piston rings, electronic components, etc. and consumables such as oil
• Minor and major overhauls.
Maintenance can either be done by in-house personnel or contracted out to manufacturers, distributors, or dealers under service contracts. Full maintenance contracts (covering all recommended service) generally cost between 1 to 2.5 cents/kWh depending on engine size, speed and service. Many service contracts now include remote monitoring of engine performance and conditions in addition to allowing for predictive maintenance. Service contract rates typically are all-inclusive, including the travel time of technicians on service calls.
Recommended service is comprised of routine short interval inspections/adjustments and periodic replacement of engine oil and filters, coolant, and spark plugs (typically 500 to 2,000 hours). An oil analysis is part of most preventative maintenance programs to monitor engine wear. A top-end overhaul is generally recommended between 8,000 and 30,000 hours of operation (see Table 2-5) that entails a cylinder head and turbocharger rebuild. A major overhaul is performed after 30,000 to 72,000 hours of operation and involves piston/liner replacement, crankshaft inspection, bearings, and seals. Maintenance intervals are shown in Table 2-5.
Maintenance costs presented in Table 2-6 are based on engine manufacturer estimates for service contracts consisting of routine inspections and scheduled overhauls of the engine generator set. Costs are based on 8,000 annual operating hours expressed in terms of annual electricity generation. Engine maintenance can be broken into fixed components that need to be performed on a recurring basis regardless of the engine run time and variable components that depend on the hours of operation. The vendors quoted all O&M costs on a variable basis for a system in baseload operation.
2.4.7 Fuels
In addition to operation on natural gas, spark ignition engines operate on a variety of alternative gaseous fuels including:
• Liquefied petroleum gas (LPG) – propane and butane mixtures
• Sour gas – unprocessed natural gas as it comes directly from the gas well.
• Biogas – any of the combustible gases produced from biological degradation of organic wastes, such as landfill gas, sewage digester gas, and animal waste digester gas
• Industrial waste gases – flare gases and process off-gases from refineries, chemical plants and steel mill
• Manufactured gases – typically low- and medium-Btu gas produced as products of gasification or pyrolysis processes Factors that impact the operation of a spark ignition engine with alternative gaseous fuels include:
• Volumetric heating value – Since engine fuel is delivered on a volume basis, fuel volume into the engine increases as heating value decreases, requiring engine derating on fuels with lower Btu content. Derating is more pronounced with naturally aspirated engines, and depending on air requirements, turbocharging partially or totally compensates.
• Autoignition characteristics and detonation tendency for fuels with lower octane rating such as propane – This is often characterized by a calculated value known as the Methane Number (MN). Different manufacturers may calculate Methane Number differently. Gases with heavier hydrocarbon components (Propane, Ethane, Butane, etc.) have a lower Methane Number as they will tend to autoignite more easily.
• Contaminants that may impact engine component life or engine maintenance, or result in air pollutant emissions that require additional control measures.
• Hydrogen-containing fuels may require special measures (generally if hydrogen content by volume is greater than 5 percent) because of hydrogen’s unique flammability and explosion characteristics.
Table 2-7 presents representative constituents of some of the alternative gaseous fuels compared to natural gas. Industrial waste and manufactured gases are not included in the table because their compositions vary widely depending on their source. They typically contain significant levels of H2 and/or CO. Other common constituents are CO2, water vapor, one or more light hydrocarbons, and H2S or SO2.
Contaminants are a concern with many waste fuels, specifically acid gas components (H2S, halogen acids, HCN; ammonia; salts and metal-containing compounds; organic halogen-, sulfur-, nitrogen-, and silicon-containing compounds such as siloxanes); and oils. In combustion, halogen and sulfur compounds form halogen acids, SO2, some SO3 and possibly H2SO4 emissions. The acids can also corrode downstream equipment. A substantial fraction of any fuel nitrogen oxidizes into NOx in combustion. To prevent corrosion and erosion of components, solid particulates must be kept to very low concentrations. Various fuel scrubbing, droplet separation and filtration steps will be required if any fuel contaminant levels exceed manufacturers specifications. Landfill gas in particular often contains chlorine compounds, sulfur compounds, organic acids, and silicon compounds, which dictate pretreatment.
Once treated and acceptable for use in the engine, emissions performance profiles on alternative fuels are similar to natural gas engine performance. Specifically, the low emissions ratings of lean burn engines can usually be maintained on alternative fuels.
We can provide Yuchai gas generator set with good quality and low price.
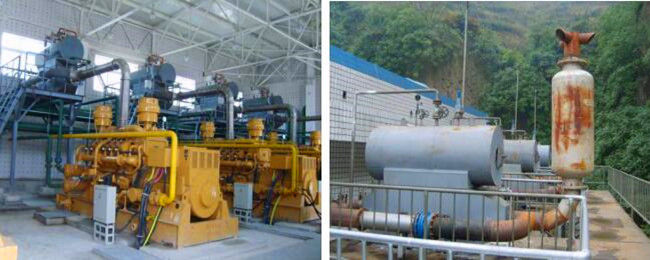
Comments