Engine Performance and Efficiency Enhancements
- startlight
- Apr 25, 2019
- 4 min read
2.4.4 Performance and Efficiency Enhancements
2.4.4.1 Brake Mean Effective Pressure (BMEP) and Engine Speed Engine power is related to engine speed and the BMEP during the power stroke. BMEP, as described above, can be regarded as an “average” cylinder pressure on the piston during the power stroke, and is a measure of the effectiveness of engine power output or mechanical efficiency. Engine manufacturers often include BMEP values in their product specifications. Typical BMEP values are as high as 320 psig for large natural gas engines and 350 psig for diesel engines. Corresponding peak combustion pressures are about 2,400 psig and 2,600 psig respectively. High BMEP levels increase power output, improve efficiency, and result in lower capital costs ($/kW).
BMEP can be increased by raising combustion cylinder air pressure through increased turbocharging, improved aftercooling, and reduced pressure losses through improved air passage design. These factors all increase air charge density and raise peak combustion pressures, translating into higher BMEP levels.
However, higher BMEP increases thermal and pneumatic stresses within the engine, and proper design and testing is required to ensure continued engine durability and reliability.
2.4.4.2 Turbocharging
Essentially all modern engines above 300 kW are turbocharged to achieve higher power densities. A turbocharger is basically a turbine-driven intake air compressor. The hot, high velocity exhaust gases leaving the engine cylinders power the turbine. Very large engines typically are equipped with two turbochargers. On a carbureted engine, turbocharging forces more air and fuel into the cylinders, which increases the engine output. On a fuel injected engine, the mass of fuel injected must be increased in proportion to the increased air input. Cylinder pressure and temperature normally increase as a result of turbocharging, increasing the tendency for detonation for both spark ignition and dual fuel engines and requiring a careful balance between compression ratio and turbocharger boost level. Turbochargers normally boost inlet air pressure on a 3:1 to 4:1 ratio. A wide range of turbocharger designs and models are used. Heat exchangers (called aftercoolers or intercoolers) are normally used on the discharge air from the turbocharger to keep the temperature of the air to the engine under a specified limit.
Intercooling on forced induction engines improves volumetric efficiency by increasing the density of intake air to the engine (i.e. cold air charge from intercooling provides denser air for combustion thus allowing more fuel and air to be combusted per engine stroke increasing the output of the engine).
2.4.5 Capital Costs
This section provides typical study estimates for the installed cost of natural gas spark-ignited, reciprocating engine-driven generators in CHP applications. Capital costs (equipment and installation) are estimated for the five typical engine genset systems ranging from 100 kW to 9 MW. These are “typical” budgetary price levels; it should also be noted that installed costs can vary significantly depending on the scope of the plant equipment, geographical area, competitive market conditions, special site requirements, emissions control requirements, prevailing labor rates, and whether the system is a new or retrofit application.
The basic generator package consists of the engine connected directly to a generator without a gearbox.
In countries where 60 Hz power is required, the genset operates at multiples of 60 – typically 1800 rpm for smaller engines, and 900 or 720 or 514 rpm for the large engines. In areas where 50 Hz power is used such as Europe and Japan, the engines run at speeds that are multiples of 50 – typically 1500 rpm for the small engines. In Table 2-4, System 4 is based on a German design, and operates at 1,500 rpm and produces 60 Hz power through a gearbox. The smaller engines are skid mounted with a basic control system, fuel system, radiator, fan, and starting system. Some smaller packages come with an enclosure, integrated heat recovery system, and basic electric paralleling equipment. The cost of the basic engine genset package plus the costs for added systems needed for the particular application comprise the total equipment cost. The total plant cost consists of total equipment cost plus installation labor and materials (including site work), engineering, project management (including licensing, insurance, commissioning and startup), and financial carrying costs during the 4 to 18 month construction period.
All engines are in low NOx configuration. System 1, a stoichiometric (rich burn) engine, uses a three-way catalyst to reduce emissions to their final level. The other systems are all lean burn engines and are shown with a SCR, CO catalyst, and continuous emissions monitoring system (CEMS) that are required in environmentally sensitive areas such as Southern California and the Northeastern U.S.
Table 2-4 provides cost estimates for combined heat and power applications based on a single unit engine. The CHP system is assumed to produce hot water, although the multi-megawatt size engines are capable of producing low-pressure steam. The heat recovery equipment consists of the exhaust economizer that extracts heat from the exhaust system, process heat exchanger for extracting heat from the engine jacket coolant, circulation pump, control system, and piping. These cost estimates include interconnection and paralleling. The package costs are intended to reflect a generic representation of popular engines in each size category. The interconnection/electrical costs reflect the costs of paralleling a synchronous generator for the larger systems. The 100 kW system uses an inverter based generator that has been pre-certified for interconnection in most areas. Labor/materials represent the labor cost for the civil, mechanical, and electrical work as well as materials such as ductwork, piping, and wiring.
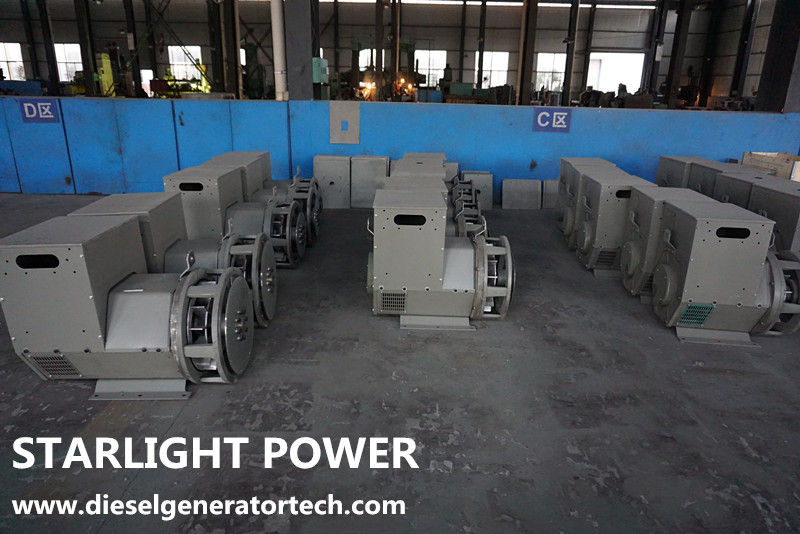
Project and construction management also includes general contractor markup and bonding, and performance guarantees. Contingency is assumed to be 5 percent of the total equipment cost in all cases. Cost estimates for multiple unit installations have lower unit costs than single unit installations.
Comments