Performance Characteristics of Natural Gas Spark Ignition Engine
- startlight
- Apr 23, 2019
- 4 min read
2.4 Performance Characteristics
Table 2-2 summarizes performance characteristics for typical commercially available natural gas spark ignition engine CHP systems over a 100 kW to 9 MW size range. This size range covers the majority of the market applications for engine-driven CHP. Heat rates and efficiencies shown were taken from manufacturers’ specifications and industry publications. Available thermal energy was taken directly from vendor specifications or, if not provided, calculated from published engine data on engine exhaust temperatures and engine jacket and lube system coolant flows. CHP thermal recovery estimates are based on producing hot water for process or space heating needs.
Most reciprocating engine manufacturers typically assign three power ratings to engines depending on the intended load service:
• Standby – continuous full or cycling load for a relatively short duration (usually less than 100 hours) – maximum power output rating.
• Prime – continuous operation for an unlimited time (except for normal maintenance shutdowns), but with regular variations in load – 80 to 85 percent of the standby rating
• Baseload – continuous full-load operation for an unlimited time (except for normal maintenance shutdowns) – 70 to 75 percent of the standby rating.
The ratings shown are for baseload operation.
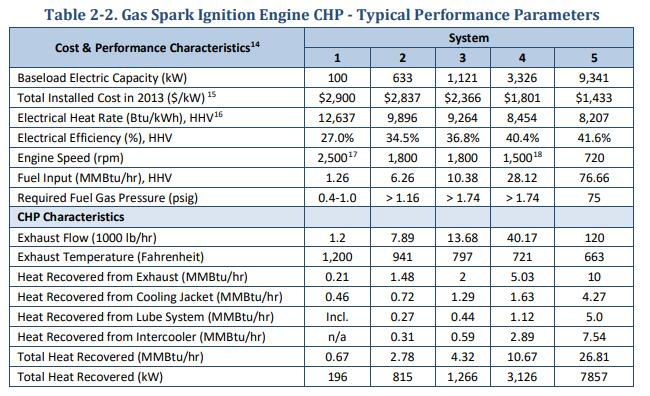

The data in the table show that electrical efficiency increases as engine size becomes larger. As electrical efficiency increases, the absolute quantity of thermal energy available to produce useful thermal energy decreases per unit of power output, and the ratio of power to heat for the CHP system generally increases. A changing ratio of power to heat impacts project economics and may affect the decisions that customers make in terms of CHP acceptance, sizing, and the desirability of selling power.
2.4.1 Part Load Performance
In power generation and CHP applications, reciprocating engines generally drive synchronous generators at constant speed to produce steady alternating current (AC) power. As load is reduced, the heat rate of spark ignition engines increases and efficiency decreases. Figure 2-3 shows the part load efficiency curve for a typical lean burn natural gas engine. The efficiency at 50 percent load is approximately 8 to 10 percent less than full load efficiency. As the load decreases further, the curve becomes somewhat steeper. While gas engines compare favorably to gas turbines, which typically experience efficiency decreases of 15 to 25 percent at half load conditions, multiple engines may be preferable to a single large unit to avoid efficiency penalties where significant load reductions are expected on a regular basis.
Diesel engines exhibit even more favorable part load characteristics than spark ignition engines. The efficiency curve for diesel engines is comparatively flat between 50 and 100 percent load.

2.4.2 Effects of Ambient Conditions on Performance
Reciprocating engines are generally rated at ISO conditions of 77 °F and 0.987 atmospheres (1 bar) pressure. (Gas turbines are rated at 59 °F.) Like gas turbines, reciprocating engine performance – measured for both output and efficiency – degrades as ambient temperature or site elevation increases.
While the effect on gas turbines can be significant, it is less so on engines. Reciprocating engine efficiency and power are reduced by approximately 4 percent per 1,000 feet of altitude above 1,000 feet, and about 1 percent for every 10°F above 77°F.
2.4.3 Engine Speed Classifications
Reciprocating engines are classified as high-, medium-, or low-speed. Table 2-3 presents the standard speed ranges in each class and the types and sizes of engines available. Engine driven electric generators typically must run at fixed (or synchronous) speeds to maintain a constant 50 or 60 Hertz (Hz) output, setting the engine speed needed within the classifications (i.e., a 60 Hz generator driven by a high speed engine would require engine speeds of 1200, 1800 or 3600 rpm versus a 50 Hz generator which requires engine speeds of 1000, 1500 or 3000 rpm).
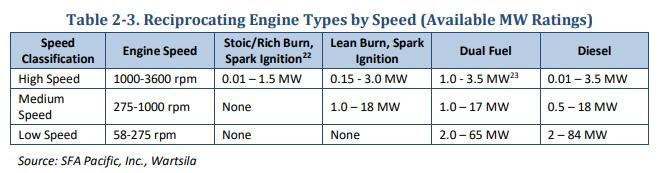
Engine power output is partly proportional to engine speed, which affords high speed engines the highest output per unit of displacement (cylinder size) and the highest power density. Consequently, high speed engines generally have the lowest $/kW production costs of the three types. The cost benefits of high speed engines must be weighed against other factors. Smaller high speed engines have lower efficiencies than large bore, lower speed engines due in part to the higher surface area to volume ratio for small cylinders resulting in slightly higher heat losses. In addition, higher speed engines tend to have higher wear rates, resulting in shorter periods between minor and major overhauls. These factors are often less important than capital costs for limited duty cycle applications.
Medium speed stationary power engines are largely derived from marine and locomotive engines.
Medium speed engines are higher in cost, but generally higher in efficiency than high speed engines.
Because of their massive physical size and high cost of installation, low speed engines are increasingly being displaced by medium and high speed engines as the primary choice for stationary power applications; with low speed engines being left to their primary market as marine propulsion engines.
Most reciprocating engine manufacturers typically assign three power ratings to engines depending on the intended load service:
• Standby - continuous full or cycling load for a relatively short duration (usually less than 100 hours) – maximum power output rating.
• Prime – continuous operation for an unlimited time (except for normal maintenance shutdowns), but with regular variations in load – 80 to 85 percent of the standby rating.
• Baseload – continuous full-load operation for an unlimited time (except for normal maintenance shutdowns) – 70 to 75 percent of the standby rating.
Comments