Remove Scale and Rust from Diesel Generator Set
- startlight
- Nov 10, 2018
- 4 min read
Scale removal methods can be used to remove chemical methods, there are the following.
1. Phosphate cleaning scale was injected with 3% trisodium phosphate solution and maintained for 10 ~ 12 hours. The scale formed soluble salts and then washed with clean water to remove the residual alkali salt and anticorrosion.
2. Alkali solution can be used to remove the scale of cast iron engine cylinder head and water jacket by NaOH 750g, kerosene 150g and water 10L, then filter it and add it to the cooling system for 10-12 hours. Then start the diesel generator and run it at full speed for 1520 minutes until the solution begins to boil and then clean it with clean water.
The aluminum cylinder head and water jacket can be mixed with sodium silicate 15g, liquid soap 2g and water 1L, then injected into the cooling system to start the engine to normal working temperature, and then run for 1 hour to release the cleaning liquid and clean it with water. For steel parts, the solution concentration can be higher, about 10% to 15% sodium hydroxide, and for non-ferrous metal parts should be lower, about 2 to 3% sodium hydroxide can be used.
3. Acid lotions commonly used to remove scale are phosphoric acid, hydrochloric acid or chromic acid. Washing with 2.5% hydrochloric acid solution, mainly make it soluble in water salts, such as CaCl2,MgCl2. The hydrochloric acid solution was added to the cooling system, and then the engine was operated at full speed for 1 h, then the solution was released. Rinse off with water more than 3 times the capacity of the cooling system. When phosphoric acid is used, the relative density of phosphoric acid (H3PO4) is 100 ml, chromic anhydride (CrO3) is 50 g, water is 900ml, heated to 30 ℃, soaked for 30 min, then washed with 0.3% dichromate. Clean, remove residual phosphoric acid and prevent corrosion. To remove the scale of aluminum alloy parts, 5% nitric acid solution or 10 ~ 15% acetic acid solution can be used.
It is suggested that the chemical cleaning solution should be selected according to the composition of scale and the material of parts.
What are the methods for removing rust from diesel generator sets
Rust is the oxide formed by the contact of metal surface with oxygen, water and acids in air, such as Fe0,Fe3O4,FeO3, which is commonly called rust. The main methods for removing rust from diesel generator are mechanical method, chemical pickling method and electrochemical acid etching method.
1. Mechanical method
Mechanical method is to remove the surface rust layer by friction and cutting between mechanical parts. Common methods include brushing, grinding, polishing and sandblasting. Individual small batch maintenance by manual steel wire brush, scraper, sand cloth brush, scratch or grind rusty later. Batches of parts or conditional units can be driven by motors or wind motors to drive all kinds of rust removal tools, such as electric polishing, rolling and so on. Sandblasting is the use of compressed air, a certain size of sand through the spray gun on the rusty surface of the parts. The craft is ready. After sand blasting, the surface is clean and has a certain roughness, which can improve the adhesion between the coating and the parts. Mechanical rust removal can only be used on the surface of unimportant mechanical parts.
2. Chemical method
This is an acid pickling method that uses chemical reactions to dissolve corrosion products from metal surface. Common acids includes hydrochloric acid, sulfuric acid, phosphoric acid, etc. The chemical used to dissolve rust products vary from metal to metal. Due to the choice of rust removal chemicals and their operating conditions are mainly determined by the types of metals, chemical composition, surface conditions and parts size accuracy and surface quality and other factors to determine.
3. Electrochemical acid etching
Electrochemical acid etching method is to put components in electrolyte and direct current electricity, through chemical reaction to achieve the purpose of rust removal. This method is faster than the chemical method, can better preserve the matrix metal, the consumption of acid is less. Generally, there are two categories, one is the removal of rust parts as anode. The other is to remove the rust of the parts as the cathode. Anodic rust removal is due to the dissolution of the metal after electrification and the tearing of the rust layer by oxygen at the anode, which results in the separation of the rust layer. Cathodic rust removal is due to the reduction of iron oxide and the tearing of rust layer by hydrogen produced on the cathode after the electricity is turned on, so that the rust is removed from the surface of the part. Cathodic rust removal is due to the reduction of iron oxide and the tearing of rust layer by hydrogen produced on the cathode after electrification. The former is easy to corrode and destroy the surface of parts when the current density is too high, so it is suitable for parts with simple shape. The latter has no over-corrosion problem, but hydrogen is easy to enter into the metal, resulting in hydrogen embrittlement, which reduces the plasticity of the parts. Therefore, it is necessary to determine the appropriate rust removal method of diesel generator set according to the specific conditions of corroded parts.
In addition, in the production practice, rust remover made from various materials can be used to treat the oil removal, rust removal and passivation in one. Except for zinc, magnesium and other metals, most metals can be used regardless of size, and spray washing and other methods can be used.
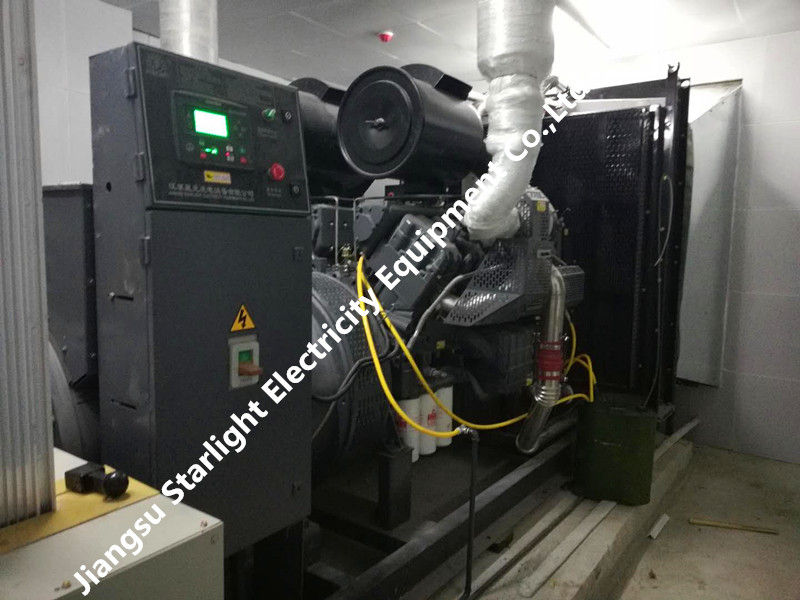
Comments