Engine Speed Regulator Adjustment - Volvo Power Generator
- startlight
- Sep 17, 2018
- 4 min read
Engine speed regulator, adjustment
The regulator has a factory setting that has been optimized to suit the most common generator set applications. Use the VODIA tool (including EMS software), to read and adjust the P, I and D sections of the engine speed regulator. Adjustment is done to obtain more stable and even engine running, and to configure the engine for specific generating set applications.
PID = Proportional, Integrating, Differentiating
P-value amplifier (Gain), amplification of the difference between the actual value and the set value.
A reduced value (Fig. 1) gives a weaker reaction to engine speed differences. Reduce the P-value to reduce oscillations arising from large differences in speed/load application.
An increased value (Fig. 2) gives a shorter response time. Increase the P section for faster compensation to large differences in engine speed/engine loading.
I-value stabilizes (Stability), reacts to the time of the speed deviation.
A reduced value (Fig. 3) increases the time taken by the system to respond after a load change. Reduce the I section to reduce the oscillations which are caused by slow application of engine loading.
An increased value (Fig 4) gives a shorter response time. Increase the I-value to provide better load response for slowly increasing loads.
D-value compensates (Derivative). Reacts to fast changes of engine speed/load.
A reduced value (Fig 4.) gives a greater sensitivity to fast changes of engine speed/load. Reduce the D-value to reduce oscillations caused by fast changes.
An increased value (Fig. 5) gives a reduced sensitivity to fast load changes. Increase the D-value to provide a better ability to compensate for fast changes.
Adjustment of PID regulator
1. Start the engine.
2. Select the “Engine with mounting and equipment” and then “Reinforcement and Stability, calibration” function groups in the VODIA tool.
3. When calibration is started, certain conditions must be met, such as that the engine must be running and must have reached a certain engine temperature.
4. Select “High” or “Low”.
High: when one is far from the nominal engine speed, i.e. to improve load response.
Low: when one is close to the nominal engine speed point, i.e. to increase stability.
5. Run the engine at the working speed and working temperature.
In cases where the engine needs to be adjusted, in-crease or reduce the values of the P and I sections until unstable (oscillating) engine speed is obtained. Then increase/decrease the parameters until the engine speed is stable again.
6. If the engine is still unstable, increase/reduce the D section until engine speed only increases slightly when load is applied (or removed), please refer to figure 6.
NOTE: The few times that the D-value may need to be adjusted include cases where the application has a flexible coupling or extremely low flywheel inertia.
7. Adjust the P and I sections again as above, if necessary.
8. Check engine response as fig. 6.
9. Repeat the procedure in the other position, “High”/“Low” if necessary.
10. To reset to factory settings, use the reset button above the PID settings.
11. Click “Continue” to finish calibration and follow the instructions to save the current settings in the control unit.
Frequency alteration, EMS2
The routine for altering the engine speed on the TAD734GE is not the same as for, i.e. D12. There is no system reset on the EMS2 unit, and the routine is therefore completely different.
With Volvo Penta CIU
If the engine is a 1500 rpm or 1800 rpm, the frequency selector must be OPEN when you start the adjustment. OPEN selects the primary engine speed, CLOSED selects the secondary engine speed.
Routine, with no system voltage applied:
1. Turn on the ignition with the starter key or switch. 2. Change the frequency selector (open or closed). 3. Send a stop request by pressing on the stop button.
The whole procedure (steps 1 to 3) may not take longer than 10 seconds.
Routine, with system voltage applied:
1. Send a stop request by pressing on the stop button.
2. Change the frequency selector (open or closed).
3. Send a stop request by pressing on the stop but-ton.
The whole procedure (steps 1 to 3) may not take long-er than 10 seconds.
With DCU
Turn on the ignition and change the parameter in the DCU.
With SAE J1939 (CAN)
Customers who use their own CAN bus-based control unit, must send certain messages to the engine (TAD734GE) in the same way as for the Volvo Pentas CIU, in order to change from 1500 to 1800 rpm (or vice-versa).
Routine, with no system voltage applied:
1. Turn on ECU.
2. Change the frequency selection in the
VP_STATUS-message (open or closed).
3. Send a stop request in a VP_STATUS-message.
The whole procedure (steps 1 to 3) may not take longer than 10 seconds.
Routine, with system voltage applied:
1. Send a stop request in a VP_STATUS-message.
2. Change the frequency selection in the
VP_STATUS-message (open or closed).
3. Send a stop request in a VP_STATUS-message.
The whole procedure (steps 1 to 3) may not take longer than 10 seconds.
NOTE: We are authorized as Volvo diesel generator OEM and can provide 85KVA to 750KVA power generator with Volvo engine. Volvo engine performance corresponds to ISO 3046, BS 5514 and DIN 6271. Engine speed governing in accordance with ISO 3046/IV, class A1 and ISO 8528-5 class G3. Besides, the engine complies with EU stage 2 emission legislation according to the Non Road Directive EU 97/68/EC.
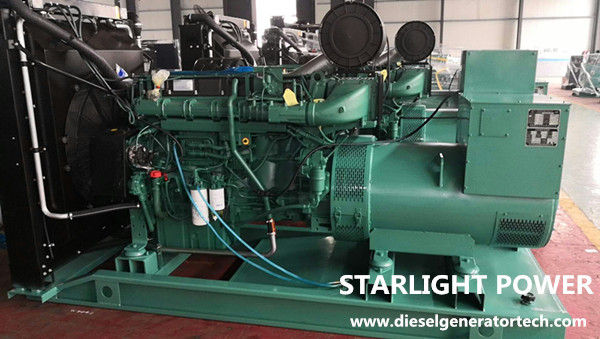
Yorumlar