General Advice on Volvo Engine - Starlight Power
- startlight
- Jul 11, 2018
- 5 min read
General advice on working with EMS engines - Volvo Engine
The following advice must be followed to avoid damage to the engine control unit and other electronics.
IMPORTANT!
The system must be disconnected from system voltage (by cutting the current with the main switch) and the starter key(s) must be in the 0 position when the engine control unit connectors are disconnected or connected.
• Never disconnect the current with the main switches when an engine is running.
• Never undo a battery cable when the engine is running.
• Turn the main switches off or disconnect the battery cables during quick charging of the batteries.
NOTICE! During normal trickle charging, it is not necessary to turn the main switches off.
• Only batteries may be used for start help. A help start device can produce a very high voltage and damage the control unit and other electronics.
• If a connector is disconnected from a sensor, be very careful to avoid allowing the contact pins to come into contact with oil, water or dirt.
Electrical Welding
1 NOTICE! Cut the current with the main switch.
IMPORTANT!
The system must be disconnected from system voltage when the engine control unit connectors are disconnected or connected.
2 Undo the two connectors from the engine control unit before any electrical welding starts. Turn the locking arm down at the same time as the connector is pulled outwards.
3 Disconnect all connections to the alternator. Connect the welder earth clamp to the component
to be welded, or as close as possible to the weld site. The clamp must never be connected to the
engine or in such a way that current can pass through a bearing.
IMPORTANT!
After welding is completed, the disconnected components, such as alternator cables and battery
cables must be connected in the correct order. The battery cables must always be connected last.
Changing the engine control unit
1 NOTICE! Cut the current with the main switch.
IMPORTANT!
The system must be disconnected from system voltage when the engine control module connectors are disconnected or connected*.
2 Remove the two connectors from the engine control unit. Turn the locking arm down at the same time as the connector is pulled outwards
3 If the new engine control unit has recently been programmed:
Start the engine and check whether any fault codes related to the engine control unit occur.
Checking the starter motor voltage
Tools:
88890074 Multimeter
General
If battery voltage falls below 24.7 V*, the starter motor will not be able to crank the engine at normal speed. A fully charged battery has an open circuit voltage of about 12.7 V.
NOTICE! * Measured on the batteries. Voltage measurement, check
1 Check that the battery voltage is at least 24.7 V when unloaded by using 88890074 Multimeter to measure between the battery poles.
2 Turn the main switch on.
3 Check that the voltage between terminal B+ on the starter motor and battery negatives connection point is the same as the battery voltage.
Checking the charging system
Generally about alternators:
The voltage output from an alternator must be limited to prevent the elecrolyte in the battery to evaporate. The alternator output is regulated (limited) by the voltage regulator in the alternator. The maximum current that the alternator can deliver at regulated voltage output depends on the alternator revolution. When the engine is started an excitation current is needed to “wake up” the alternator.
NOTICE! It is the consumers (batteries included) which decides the output current from the alternator.
Measurements
1 Engine off.
2 Use 88890074 Multimeter to do a voltage measurement over the battery. The nominal voltage
over a full loaded battery is approx. 12.7 V.
3 Engine on. Run at 1500 rpm.
4 Use 88890074 Multimeter to do a voltage measurement over the battery and also over the alternator.
The nominal charging voltage over the batteries should be approx. 27.8-28.6 V.
Tools:
88890074 Multimeter
Fault tracing charging system
Battery check
1 Check that all connectors at the battery are correctly assembled.
2 Check the condition of the cables to the battery.
3 Check the water level in the battery.
4 Check, if possible, the specific gravity of all cells. when no charge
1 Check the alternator belt tension.
2 Check that all connectors at the alternator and at the battery are correctly assembled.
3 Check the condition of all cables in the charging system.
4 Regulator fault. Replace regulator. when undercharge
1 Check the alternator belt tension.
2 Check that all connectors at the alternator and at the battery are correctly assembled.
3 Check the condition of all cables in the charging system.
4 Regulator fault. Replace regulator. when overcharge
1 Probably regulator fault. Replace regulator.
Rail pressure measurement
This measurement is used for measuring the rail pressure. For example if the engine doesn´t start this measurement can show the rail pressure while the engine is cranking. If it is air in the system the rail pressure could be too low for the engine control unit to activate injection.
1 NOTICE! Starter key in position 0.
2 Undo the connector from the sensor.
3 Connect adapter cable (885675) between the sensor and the EECU.
4 Use multimeter (88890074) for voltage measurement. Connect the COM from the multimeter to measurement point 1. Connect V from the multimeter to measurement point 2.
5 NOTICE! Starter key in position I. The multimeter should now show 0.5 Volt which is equal to 0 Mpa (0bar).
6 When cranking the engine, read the voltage value on the multimeter and look in the table which pressure the voltage equals.
NOTICE! To activate injection a rail pressure of at least 25 MPa (250 bar) is demanded.
Manual fault tracing in bus cables
Tools:
88890074 Multimeter
IMPORTANT!
Cut the current with the main switch before the cables are disconnected.
Use the multimeter to check the bus cables. The conductors in the bus cables should not be in contact with each other. Disconnect a bus cable at each end and measure the resistance between the pins to check this. The multimeter should show infinite resistance between each pin. If the resistance is less than infinite, there is a fault.
Measuring the engine cables
Two types of measurements are done on the engine cable harness, both resistance measurement and oltage measurement.
The measurements are done to ensure that no open circuits or short circuits occur.
If there is an open circuit, the resistance is infinite, and if there is a short circuit, it is close to zero. The resistancevalues given in the workshop manual are approximate, and should be regarded as guidelines.
NOTICE! When resistance measurement is done, the engine should be stopped and system voltage should be cut off with the main switch. All resistance measurement is done at +20 °C (68 °F) and with a cold engine.
We can provide Cummins generator, Perkins generator, Volvo generator, Deutz generator,Yuchai generator and Ricardo generator with good quality. Our products meet international standard ISO 8528.
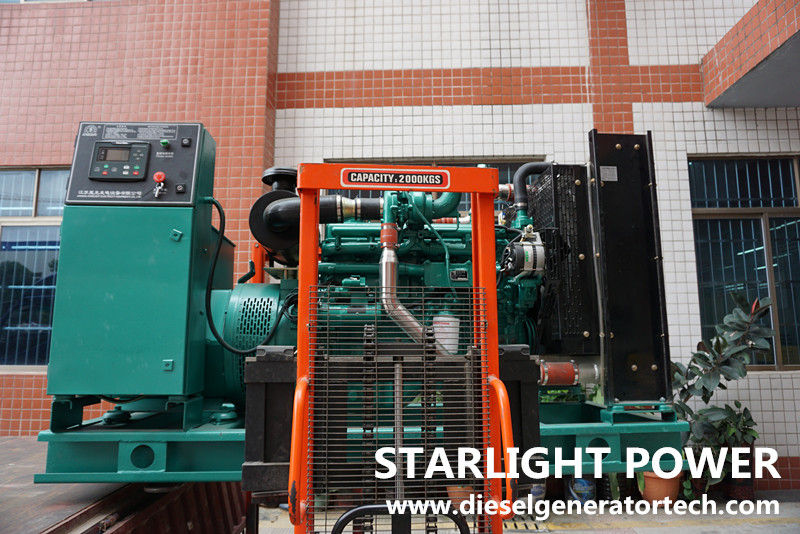
Comments